Fire Safety Policy
1. POLICY OVERVIEW
2. AUTHORITY AND RESPONSIBILITY
3. FIRE EMERGENCY RESPONSE
4. FIRE PREVENTION AND TRAINING
5. ELECTRICAL EQUIPMENT AND APPLIANCES
6. FIRE DETECTION SYSTEMS
7. FIXED FIRE SUPPRESSION SYSTEMS
8. PORTABLE FIRE EXTINGUISHERS
Click to download the Fire Safety Policy.
The Fire Safety Policy was developed to ensure the health and safety of faculty, staff, students, and visitors while also ensuring compliance with appropriate regulatory agencies. This Policy utilizes regulatory compliance objectives, as well as, industry best practices, to establish fire prevention guidelines across the MBL. The intent of this Policy is to ensure activities that create a fire risk or may contribute to conditions that favor the spread of fire are identified and mitigated.
This policy defines individuals’ actions and responsibilities associated with the MBL buildings located in Woods Hole, MA in the event of a fire emergency. All employees of MBL must be aware of the location of the fire alarms, location of fire extinguishers, familiar with both primary and secondary evacuation routes for their area and participate in yearly fire safety training. This plan includes the following information; procedure once a fire is detected, evacuation locations, and proper use of a fire extinguisher.
In addition, this policy provides information on use of electrical equipment and appliances, MBL Fire Detection Systems, MBL Fixed Fire Suppression systems and monitoring/tracking of MBL’s portable fire extinguishers.
2. AUTHORITY AND RESPONSIBILITY
All individuals at the MBL should take responsibility for promoting a safe working environment in their area. Upon hire and annually, all employees of MBL are provide fire safety training. As outlined below specific individuals and groups share heightened responsibility for the MBL’s Fire Safety Policy.
2.1 Environmental Health and Safety (EHS) Manager is responsible for:
- Developing the Fires Safety Policy and reviewing annually for compliance;
- Conducting annual facility inspections;
- Coordinating Fire Drills;
- Conducting Fire Response Team training;
- Preparing Fire Drill Critique Reports; and
- Providing training for employees covered under this policy.
2.2 Plant Operations and Maintenance Manager is responsible for:
- Care, maintenance and testing of Fire Detection and Fire Suppression systems in accordance with NFPA Codes and Standards;
- Initialing a fire watch when a fire detection system is impaired;
- Conducting inspections of the fixed fire suppressions system;
- Coordinating the Red Tag Permit systems with signage and notifications for system impairment;
- Oversee monthly inspection on portable fire extinguishers as required by the Occupational Safety and Health Administration (OSHA);
- Retaining all documents related to fire detection and suppression systems which include testing, maintenance and inspection; and
- Oversee outside Contractors used for inspection/maintenance of fire protection systems.
2.3 Fire Response Team is responsible for:
- Immediate response to Fire alarm;
- Locating and assessing Fire or False Alarm;
- Ensuring complete building evacuation;
- Working with Falmouth Fire Department; and
- Performing annual Fire Drills and training.
2.4 Department Managers are responsible for:
- Ensuring that their staff understand and adhere to this policy;
- Following purchasing recommendations outlined in this policy;
- Minimizing the risk of fire as a result of activities under their control; and
- Removing items from service that do not conform to this policy.
2.5 Employees are responsible for:
- Participating in annual Fire Drills and training; and
- Following the Fire Safety and Evacuation plan.
2.6 Licensed Contractors are responsible for:
- Performing appropriate inspection, testing and maintenance of the fire detection and suppression systems when scheduled by POM;
- Providing documentation to POM when inspections and maintenance completed; and
- Complying with the procedures outlined in this policy.
3. FIRE EMERGENCY RESPONSE
In the event of an actual fire, this section breaks down the specific procedures to follow from the initial response actions to the use of a fire extinguisher. In addition, this section includes the actions of the Fire Response Team to assist with evacuation and locating (and possibly extinguishing) the fire.
3.1 Fire Action Procedures
Upon detection or notification of heavy smoke or flames, employees at MBL will follow the use of the acronym R-A-C-E for response actions.
- Rescue: If safe, RESCUE anyone in immediate danger;
- Alarm: Activate nearest fire ALARM, Call 9-911 for Falmouth Fire Department and then call x7911 for MBL Security;
- Contain: CONTAIN smoke and fire to confined area by closing all doors to rooms, stairwells and corridors; and
- Evacuate/Extinguish: EVACUATE to designated area using appropriate route. See Section 3.3 for locations. Do not use elevators. EXTINGUISH small fire only if trained and if safe.See Section 3.4 for proper use.
Note: In the event of a “burning smell” but no visible smoke or flames, call MBL Security at x7217.
3.2 Fire Response Team
The Fire Response Team consists of selected members of the MBL staff, which are trained to provide immediate support in the event of a fire at MBL. The Fire Response Team consists of: Security Staff, Plant Operations and Maintenance (POM) Staff, and the Environmental Health and Safety Manager.
3.2.1 Fire Alarm Sounding
When a fire alarm is activated due to a fire, Security Staff will make the following notifications:
- Notify 911 and advise them on the fire location;
- Contact the Director of Facilities and Services;
- Contact the Environmental Health and Safety Manager; and
- Contact the Assistant Director of Facilities and Services.
All available Security Staff and POM Staff will be notified to report to the scene of the fire (main entrance of building). The primary communication will take place utilizing Channel 1 on the radios (emergency channel).
3.2.2 Response to Fire
On scene, duties of the Fire Response Team will include:
- Coordinating responsibilities by a senior team member onsite;
- Prior to entering building, team members must verbally inform either a supervisor or a senior team member;
- Following the R-A-C-E procedures (see section 3.1);
- Assisting with evacuation of individuals from building to designated location;
- Attempting to extinguish a small fire using the P-A-S-S procedure for fire extinguishers (see section 3.4);and
- Meet and provide critical information to Fire Department upon arrival.
3.2.3 “All Clear” Notification
Once the building has been evacuated of MBL personnel and fire has been extinguished or triggered alarm deactivated, the following may occur:
- First all members of the Fire Response Team must either meet outside or communicate via radio to close out the Fire Team’s response to fire alarm;
- In event of a false alarm, individuals may return to work upon an “All Clear” from the senior team member;
- In event of a small fire, an “All Clear” will need to be first provided by the Fire Department to the senior team member. Who then may provide an “All Clear” to MBL personnel.
- Under no circumstances may a MBL employee enter building until an “All Clear” command is provided.
3.3 Evacuation
If an alarm sounds, evacuate the building promptly only pausing to close doors. The evacuation routes are posted in each hallway with a primary and secondary route. Use nearest exit to outside. Upon exiting building, individuals should congregate at the designated evacuation area for their building as follows:
Evacuation Area: QUAD
Buildings: Rowe, Homestead, ESL, Starr, Loeb
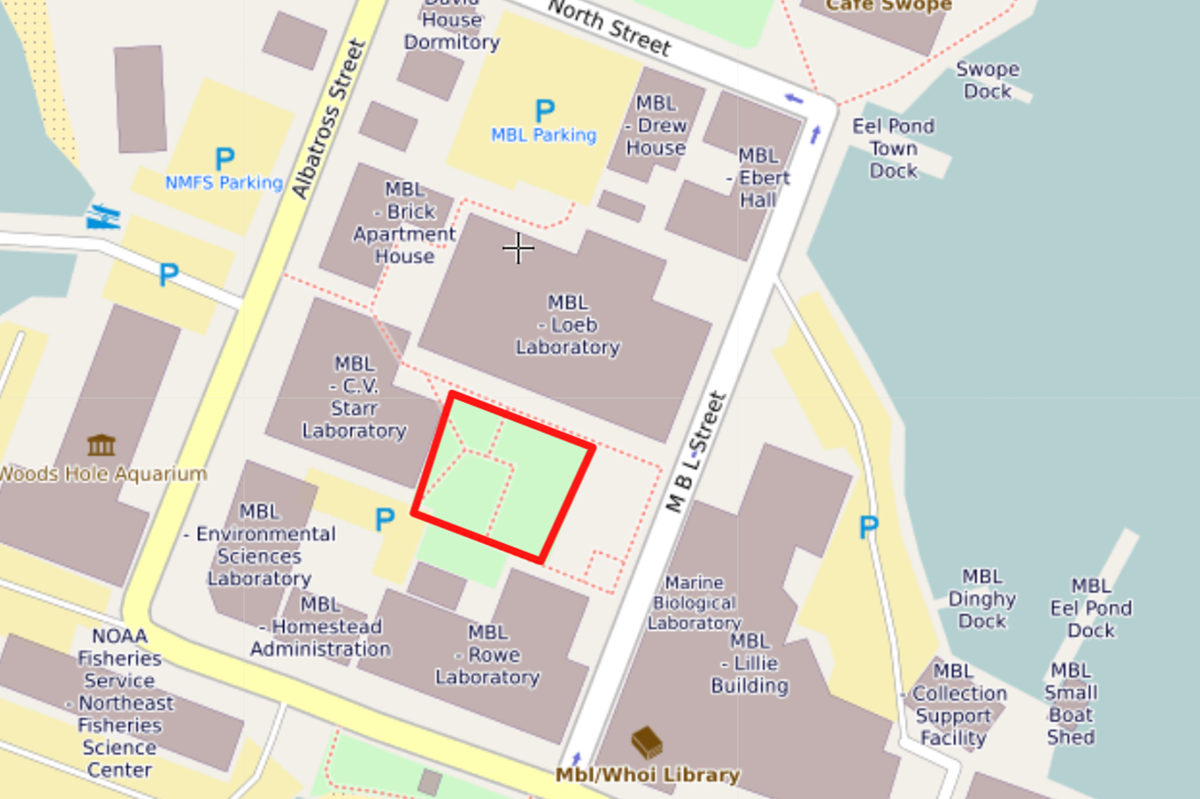
Evacuation Area: Lillie Rear Parking Lot
Buildings: Lillie, Marine Resources Center (MRC), Collection Support Facility (CSF), Candle House
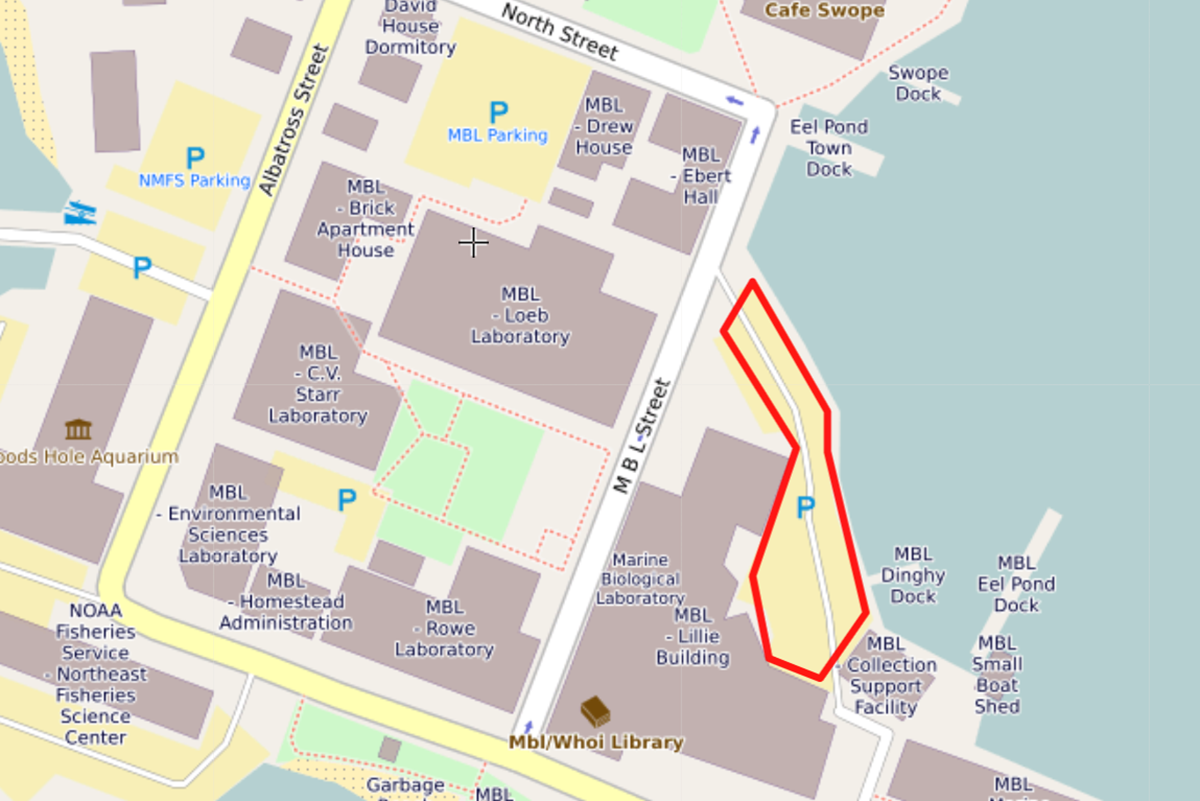
Evacuation Area: Swope Parking Lot
Buildings: Swope, Carpenter Shop
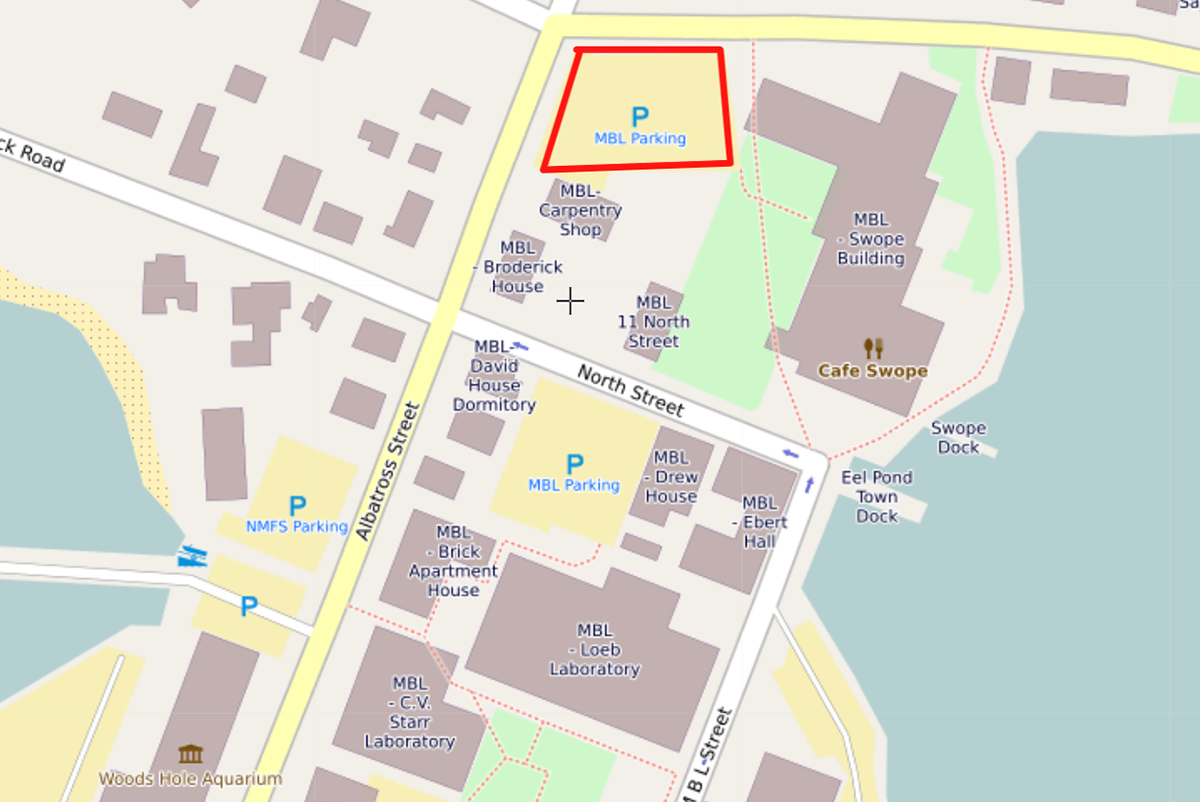
Evacuation Area: Loeb Parking Lot
Buildings: Animal Care Facility (ACF), Broderick House, Housing; Ebert, Drew, Brick, Veeder, David, 11 North
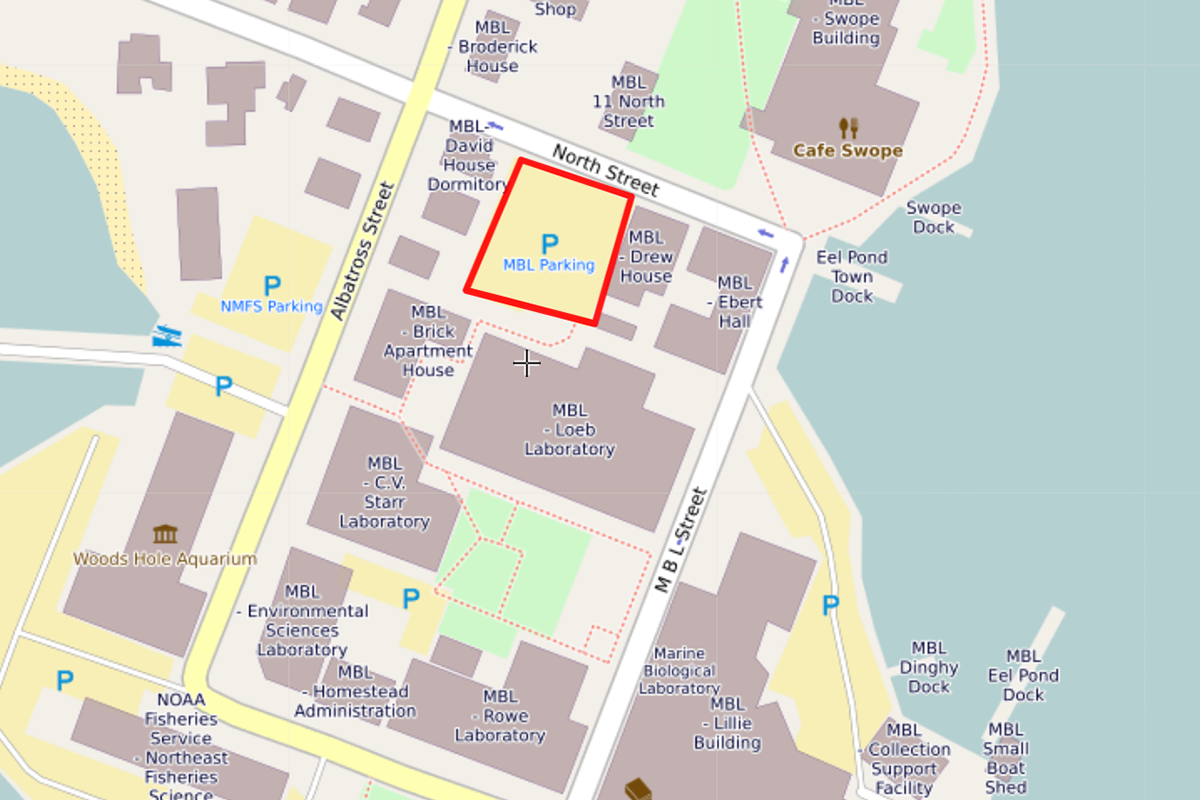
Note: If the MBL Fire Response Team determines that the designated evacuation area noted above is not safe, individuals will be instructed to another location. Individuals may only re-enter building after all clear is announced by the Fire Response Team.
3.4 Fire Extinguishers
If an employee has been trained and the fire is small and confined, an employee may attempt to extinguish the fire using an appropriate fire extinguisher. Training includes understanding which fire extinguisher is appropriate for the fire and operating the extinguisher using the P-A-S-S procedure.
3.4.1 Types of Fire Extinguishers
Each fire extinguisher is marked with a “Class” designation for the intended use. The following fire extinguishers are present at the MBL:
- ABC: Used on any type of fire combustibles (wood, paper, cloth), flammable liquids (gas, oil, solvents), electrical fires;
- BC: Used on flammable liquids (gas, oil, solvents), electrical fires;
- CO2: Used on electrical fires; and
- K: Used for kitchen fires.
3.4.2 Operating a Fire Extinguisher
With the appropriate fire extinguisher in hand, position yourself for easy exit and escape approximately 6-8 feet away from the fire. Operate the fire extinguisher using the acronym P-A-S-S as described below.
- Pull: Pull the pin;
- Aim: Aim the nozzle low at the base of the fire while standing about 6-8 feet away from the fire;
- Squeeze: Squeeze the handle with opposite hand; and
- Sweep: Sweep slowly side to side at the base of the fire.
Note: Do not attempt to extinguish a fire that continues to spread, exit the building immediately.
4. Fire Prevention AND TRAINING
To instill a strong culture of safety, MBL is committed to provide both annual fire drills and annual fire safety training to all faculty and staff. The training will include discussion on fire prevention with emphasis on activities that create a fire risk or may contribute to conditions that favor the spread of fire. Specific electrical equipment guidance is provided in Section 5.
4.1 Fire Prevention
Prevention is the key to fire safety with employees constantly on the alert to prevent conditions that could result in fire. Below are some of the most basic fire prevention strategies which should always be followed:
- Observe MBL’s No Smoking in the Building Policy;
- Keep and store properly flammable or combustible materials away from heat sources;
- Keep all work areas clean, and do not allow combustible materials, such as cardboard boxes and paper storage to accumulate;
- Keep all exits and corridors free of obstructions;
- Electrical cords need to be repaired or replaced if damaged, frayed or cracked. Contact POM when found x7776;
- Extension cords shall not be used unless approved by POM;
- Do not overload electrical outlets or run electrical cords under carpets or through doors;
- Do not wedge, prop or tie doors open. Do not block doors;
- Do not block access to emergency equipment i.e. fire extinguishers, fire alarm pull stations, fire standpipe valves etc;
- Do not store items within 18” of an automatic sprinkler head; and
- Report potential fire and safety hazards to the Safety Office at x7424.
- Use caution when combining electrical appliances with aquatic systems.
4.2 Training
Environmental Health and Safety shall facilitate training of employees covered by this policy. The training program shall, at a minimum, cover the following:
- Understanding R-A-C-E procedures;
- Use of a Fire Extinguisher with P-A-S-S procedures; and
- Fire prevention.
Employees shall be required to participate in annual training which will typically coincide with the annual Chemical Safety Training. New employees will need to take training through the MBL Safety Office upon hire. All training shall be documented with records maintained by Environmental Health and Safety.
Annual Fire Drills are conducted for each of the main MBL buildings. These drills will not only involve the evacuation of occupants of each building but test the response/duties of the Fire Response Team. The Safety Office completes an MBL Facility Fire Drill Critique Report to document the event and make recommendations for improvements.
5. ELECTRICAL EQUIPMENT AND APPLIANCES
The use of electrical appliances such as space heaters, extension cords and laboratory equipment pose a significant fire risk when not used appropriately or used when in need of repair/replacement. All equipment and appliances identified in this policy shall be designated as approved with a nationally recognized testing laboratory mark, such as from Underwriters Laboratories (UL).
5.1 Small Electrical Appliances
A small appliance is a portable or semi-portable machine, generally used on table-tops, counter-tops, or other platforms, to accomplish a household task. Examples include the following: hot plates, microwave ovens, toaster ovens, toasters, fans and coffeemakers.
Toaster ovens, toasters, and hot plates are prohibited in MBL dorms or at individual workstations. These devices are only allowed in dining areas or designated kitchenette/break rooms. All appliances allowed for use and utilized in office breakrooms or kitchenettes shall carry a commercial use listing. These devices must not be left unattended during use.
Personal coffee makers (four cups or less) that do not incorporate a hot plate may be used in private offices or workstations.
Appliances shall be plugged directly into an outlet. If more than two appliances with a cumulative wattage of more than 1,500 watts are plugged into a single wall outlet, a power strip designated as approved with a nationally recognized testing laboratory mark (such as UL) with a built-in circuit breaker shall be used. In addition to the appliance itself, both the cord and plug shall be undamaged (cord not taped or covered, plug intact and without conductors showing, no cracks or breaks in cord or plug).
5.2 Space Heaters
Space heaters with electrical heating elements that glow red-hot and fuel powered (e.g., kerosene, propane) are prohibited from MBL buildings. Only electric space heaters with water/oil fluid enclosed heating elements or ceramic covered heating elements which provide radiant heat are allowed for use. Space heaters are to be approved by the Environmental Health and Safety office.
The use of electric space heaters as a temporary measure is permitted, if the following guidelines are followed:
- Space heaters cannot be operated within three feet of combustible materials including waste baskets, furniture, coat racks, or draperies;
- Items with an ignition source, including space heaters, shall not be placed in areas where flammable or explosive vapors may be potentially found;
- Space heaters shall not exceed 110 volts and shall not be rated for more than 1,500 watts; 1,500 watt space heaters shall be plugged into an electrical outlet that is rated for 20 amps or greater;
- Space heaters shall be designated as approved with a nationally recognized testing laboratory mark;
- Space heaters shall have a thermostat that shuts off when a certain temperature is reached which means heaters without thermostats (i.e., simple “on/off” or “high/low”) are not permitted;
- Space heaters shall have functional tip over protection (i.e., space heater shall turn off automatically if tipped over);
- Space heaters shall have overheat protection (i.e., space heater will automatically shut the unit off if there is an overheat situation);
- Space heater may only be located on the floor. It is prohibited to place the space heater on file cabinets, desks, or tables;
- Space heaters shall plug directly into an electrical outlet. It is prohibited to plug the space heater into an extension cord or power strip;
- Space heaters shall not be located in high traffic areas or used in dusty environments (e.g., workshops);
- Space heaters shall always be turned off and unplugged when not in use; and
- Space heaters shall not be left running unattended.
5.3 Extension Cords and Power Strips
Extension cords and power strips shall be inspected for damage to the outer insulation prior to use. If damage extends beyond the outer layer of cord (i.e., if the conductor is exposed), then the extension cord shall be discarded.
Extension cords and power strips shall be plugged into a wall outlet and may not be plugged into another extension cord or power strip. Extension cords may never be used in place of permanent wiring and may only be used for a temporary period of up to 90 days. Extension cords shall be unplugged when not in use.
Never run cords under doors, rugs, or carpeting; through walls; or above lay-in ceiling tile.
Extension cords and power strips shall be designated as approved with a nationally recognized testing laboratory mark and used within the manufacturer’s guidelines. Industrial/commercial grade equipment, power tools, and other high-current devices may not be plugged into power strips or extension cords unless they are designated as approved with a nationally recognized testing laboratory mark for industrial/commercial use (the manufacturer’s guidelines will specify the rating of the power strip). The use of household extension cords (two prong) and non-multi-plug adapters (e.g., one-to-three plug adapter) are not permitted.
5.4 Electrical Equipment and Aquatic Systems
Electrical appliances are used in conjunction with aquatic systems at MBL, which poses potential hazards associated with electricity and water. Appliances should be configured with the anticipation of system failure, and the appropriate preventative measures. Some electrical appliances used with aquatic systems are submersible water heaters, UV lights, and any other general electrical appliances used in the lab. Submersible water heaters specifically have been known to start fires when used improperly. To learn more about usage of these systems, refer to the Use of Submersible Heaters document, which can be found on the MBL website.
6. FIRE DETECTION SYSTEMS
The MBL Fire Detection System includes the following components, but not limited to:
- Fire alarm panels;
- Fire alarm annunciator panels;
- Detection devices, such as heat and smoke detectors; and
- Manual pull stations.
Fire alarm systems are installed as needed on a per building basis. Buildings classified as institutional, schools, hotels, dormitories, and high-rises (greater than 80 feet) are required by local Falmouth and MA code to have fire alarm systems installed.
In sleeping areas, the National Fire Protection Association (NFPA) under NFPA Chapter 72, Section 6-3.4, the National Fire Alarm Code, requires: “Where audible appliances are installed to signal sleeping areas, they shall have a sound level of at least 15 dBA above the average ambient sound level or 5 dBA above the maximum sound level having a duration of at least 60 seconds or a sound level of at least 70 dBA, whichever is greater, measured at the pillow level in occupiable area.” See Appendix A: MBL Campus Buildings Fire Protection
6.1 Inspection and Testing
The monthly inspection and testing of fire detection systems shall be in accordance with Chapter 72 “National Fire Alarm Code” of the National Fire Protection Association (NFPA).
All fire detection systems shall be tested at least annually by a American Services our private contractor knowledgeable in the operations and function of the system. Criteria for the annual testing shall be in accordance with NFPA Chapter 72 “National Fire Alarm Code”.
6.2 Fire Detection Impairment Policy
All fire detection systems and their components that require being shut down due to maintenance and/or testing shall follow the appropriate notification and fire watch procedures and then reactivation procedures as defined below.
6.2.1 Before Shutdown
Before the shutdown of fire detection equipment, the project manager, facility manger, or supervisor shall put in a work request with Plant Operations and Maintenance to request fire detection be taken out of service. Shutting down fire detection equipment shall be planned and limited to an eight hour time period. All requests in excess of eight hours shall be reviewed and approved by Environmental Health and Safety.Red Tag Permit will be issued by POM for approved work.
6.2.2 Notification Process
For fire detection system shutdowns greater than one hour, a representative from Plant Operations and Maintenance:
- Notify the Security to inform them of fire detection system impairment; and
- Notify the appropriate monitoring station to inform them of fire detection system impairment.
For fire detection system shutdowns greater than eight hours, the project manager, facility manger, or supervisor shall also notify Environmental Health and Safety.
6.2.3 During the Shutdown – Fire Watch
For all fire detection system shutdowns in excess of four hours in unoccupied buildings, a fire watch shall be implemented by the original person requesting the fire detection system shutdown. All MBL employees performing the fire watch shall be trained by Environmental Health and Safety in Fire Safety and Evacuation. When outside contractors are performing the fire watch, they shall be knowledgeable in the following:
- Portable fire extinguisher procedures;
- Procedures for reporting an emergency;
- Evacuation procedures; and
- Hazard recognition.
The fire watch shall consist of the following during the impairment:
- Periodically inspecting the areas and rooms within the affected building(s) to ensure hazards do not exist;
- Ensuring adequate fire protection equipment is available and in working condition; and
- Limiting hazardous work practices such as welding, cutting, brazing, or the usage of open flame.
6.2.4 Restoring the System
Upon completion of the work, the Plant Operation and Maintenance Manager or designee shall:
- Restore all fire detection back into automatic service;
- Reset the fire alarm system in normal operating condition;
- Notify Security to inform them of the reactivation of the fire detection system;
- Notify the applicable monitoring station to inform them of the reactivation of the fire detection system; and
- Notify Environmental Health and Safety that the system has been restored.
6.3 Documentation
All documentation related to monthly inspections, annual testing, and/or maintenance of fire detection systems shall be maintained by Plant Operations and Maintenance.
7. FIXED FIRE SUPPRESSION SYSTEMS
This MBL fixed fire suppression system includes the following components, but not limited to:
- Sprinkler systems; See Appendix A: MBL Campus Buildings Fire Protection
- Standpipe and fire hose systems (Class I systems); and
- Fixed chemical extinguishing systems.
7.1 Inspection, Testing and Maintenance
All fixed fire suppression systems shall have the appropriate inspection, testing, and maintenance performed by an outside licensed contractor in accordance with the Town of Falmouth and MA fire code and National Fire Protection Association. Documentation shall be kept and available for review for all inspections, testing, and maintenance of fixed fire protection systems.
All sprinkler systems installed in new construction or during the upgrade of an existing system shall have an acceptance test completed prior to being placed into service. The testing shall be arranged for by the project manager or in conjunction with the contractor installing the system. Upon scheduling of the testing, the project manager shall notify the MBL’s insurance provider and EHS.
7.2 Impairment Procedures
Shutting downfixed fire suppression systems shall be planned in advance. All equipment such as excavating, pipe plugs, repair parts, and personnel shall be ready prior to taking the system out of service.
Before the shutdown of the fire protection equipment, the supervisor of theemployeeperforming the work shall request the shutdown by submitting a work order to the Plant Operations and Maintenance Manager at 508-289-7773 at least 48 hours in advance.
7.2.1 Notification
Before the shutdown of the fixed fire suppression system, a representative from Plant Operations and Maintenance shall:
- Ensure proper steps are taken to shut down any fire alarm systems. Refer to theFire Detection Systemssection 6.0; and
- Notify the following agencies as to the reason of theimpairment and the approximate amount of time the system will be impaired:
- The monitoring service
- MBL’s insurance provider
- Environmental Safety and Health
If requested, a representative of POM and EHS can tour the site. The purpose of the tour is to ensure that proper precautions are taken andhazardous processesare restricted. If necessary, EHS will coordinate with the supervisor or project manager to arrange for temporary protection such as charged hose lines, the setting up of temporary sprinkler protection, extra extinguishers, or to establish a fire watch for the building or area.
If the project involves any type of cutting, welding, or brazing, the supervisor or designee shall obtain a Hot Work Permit. Refer to theHot Work Managementpolicy.
When all precautions are taken, the manager or designee from Plant Operations and Maintenance department shall issue a Red Tag Permit. The permit shall be posted on the main fire panel or annunciator for the equipment which has been impaired.
7.2.2 During the Shutdown
During the shutdown of the fixed fire suppression equipment, the supervisor of the employee performing the work shall maintain the following restrictions:
- Limit the practice of hazardous processes (e.g., usage of open flame, mixing and transferring of chemicals); and,
- Restrict cutting, welding, or brazing within the building, as determined by risk.
7.2.3 Fire Watch
All MBL employees and contractors performing the fire watch shall be trained in Fire Safety and Evacuation. Outside contractors performing fire watch shall have knowledge of the following:
- Portable fire extinguisher procedures;
- Procedures for reporting an emergency;
- Evacuation procedures; and
- Hazard recognition.
The fire watch shall conduct the following during the impairment:
- Periodically inspecting the areas and rooms within the affected building(s) to ensure hazards do not exist;
- Ensuring adequate fire protection equipment is available and in working condition; and
- Limiting hazardous work practices such as welding, cutting, brazing, or the usage of open flame.
7.2.4 Restoring the System
Upon completion of the work, Plant Operations and Maintenance shall be responsible for:
1. Notifying the following agencies that the system has been restored:
- MBL’s insurance provider;
- MBL Security;
- The monitoring service; and
- Environmental Health and Safety
2. Ensuring that all components of the fixed fire suppression system are placed back into automatic service.
If sprinkler protection was impaired, Plant Operations and Maintenance and the service contractor are responsible for:
- Ensuring that sprinkler control valves are locked in the open position;
- Resetting the fire alarm system in normal operating condition; and,
- Removing the Red Tag Permit or Sprinkler System Shutdown Permit from the equipment and fire panel/annunciator.
7.3 Emergency Shutdown
When a system is taken out of service unexpectedly, such as sprinkler pipes breaking or otherwise physically damaged, stabilize the situation and precautions outlined in the previous sections.
7.4 Documentation
All inspection, testing, and maintenance reports of fixed fire suppression systems shall be maintained by Plant Operations and Maintenance.
8. PORTABLE FIRE EXTINGUISHERS
All portable fire extinguishers shall be distributed, maintained, inspected and tested in accordance with this following sections.
8.1 Monthly Inspection
All portable fire extinguishers provided by the MBL shall be placed into a monthly inspection program. The monthly inspection shall be performed by the Plant Operations and Maintenance department and/or department safety representative.
The monthly inspection shall include a check of the following items:
- Confirm the extinguisher is in the proper location;
- Confirm the extinguisher is not obstructed;
- All seals and pins are in place and have not been removed or tampered with;
- If applicable, check gauge to ensure that the pressure is within the operable range;
- Examine the extinguisher for obvious signs of physical damage, leakage, corrosion or clogged nozzles; and
- Ensure that a current service tag is present on extinguisher.
When the appropriate personnel discover that the extinguisher is damaged, missing, or inoperable, they shall remove the extinguisher from service and replace it with an extinguisher of the same rating and size. If the extinguisher is obstructed, the appropriate department personnel shall contact the person whose materials are obstructing the extinguisher and have them remove the materials immediately or make arrangements to relocate the extinguisher.
Upon completing the monthly inspection, the appropriate department personnel shall date and initial the service tag.
8.2 Annual Maintenance
All portable fire extinguishers shall have an annual maintenance check completed by a contractor that is licensed by the Commonwealth of Massachusetts. All maintenance and hydrostatic testing performed by the service shall be in accordance with Chapter 10 “Portable Fire Extinguishers” of the National Fire Protection Association.
The scheduling of annual maintenance inspections is the responsibility of Plant Operations and Maintenance.
8.3 Fire Loading
The following is a description of the three degrees of fire loading present at MBL.
Light (Low) Fire Load: An Occupancy in which Class A combustible materials including furniture, window treatments, and its contents is of minor quantity. Small amounts of Class B flammable liquids such as duplicating and cleaning solvents are included provided that they are kept in closed containers and stored properly.
Ordinary (Moderate) Fire Load: An occupancy in which Class A combustibles, Class B flammable liquids, and Class C energized electrical equipment are in greater amounts than expected under a low hazard. These locations include dining areas, storage areas and assembly halls.
Extra (High) Fire Load: An occupancy in which the total amount of Class A combustibles, Class B flammable liquids, and Class C energized electrical equipment present is over and above those classified as moderate hazard. Theses occupancies and areas include laboratories, cooking areas, trade shops, and warehouses.
8.4 Extinguisher Labels and Types
All fire extinguishers shall have a label affixed to the front of the extinguisher showing operating instructions and the extinguisher rating. A pictogram, located on the fire extinguisher label, can be used for identifying the extinguisher’s rating.
Pressurized Water: The pressurized water extinguisher is the most popular type of extinguisher used for extinguishing Class A fires.
Carbon Dioxide: The carbon dioxide fire extinguisher is primarily used in areas where the potential for Class B and Class C fire loads exist.
Multi-Purpose Dry Chemical: The dry chemical fire extinguisher is used in areas where Class A, Class B or Class C hazards are encountered. This type of fire extinguisher is most common across the MBL buildings.
Extinguishing Agents for Combustible Metals: There is no single extinguishing agent or powder that will control or suppress all combustible metal fires. The type of extinguishing agent in a particular area is based on the type of combustible metals being used.
8.5 Distribution of Portable Fire Extinguishers and Mounting
The following points give the travel distances a person should not exceed in order to obtain a fire extinguisher. (Type of Hazard; Basic Minimum Extinguisher Rating; Maximum Travel Distance to Extinguishers)
- Any; A; 75 feet
- Light (Low); 5-B; 30 feet
- Light (Low); 10-B; 50 feet
- Ordinary (Moderate); 10-B; 30 feet
- Ordinary (Moderate); 20-B; 50 feet
- Extra (High); 40-B; 30 feet
- Extra (High); 80-B; 50 feet
- Any; C; 50 feet
- Any; D; 75 feet
All portable fire extinguishers shall be installed on brackets or mounted in wall cabinets. Extinguishers having a gross weight not exceeding 40 pounds shall be installed so that the top of the extinguisher is not more than five feet from the floor. Extinguishers having a gross weight exceeding 40 pounds shall be installed so the top of the extinguisher is not more than three and one half feet above the floor. The bottom of the extinguisher, in either case, shall not be less than four inches above the floor.
Where the extinguisher is likely to be obscured, a sign shall be installed marking the location of the fire extinguisher. The sign shall be visible from a distance of at least 50 feet if the extinguisher cannot be relocated.
8.6 New Fire Extinguishers
The installation of a new fire extinguisher must be approved by the Health and Safety department, with knowledge of the potential hazard(s) present in the designated location. When extinguishers are offline due to servicing, they must be temporarily replaced with a spare unit of the same type and rating. When an extinguisher is used or fails inspection, the Facility Manager is responsible for replacing it with a unit of the same type and rating.
Appendix A: MBL Campus Buildings Fire Protection
MBL Campus Housing Facility Fire Safety Systems:
Location | Primary Use | Alarm Systems | Beds Protected by Fire Detection Systems | Pull Stations Present | Beds Protected by Sprinkler Systems | Carbon Monoxide Detection |
---|---|---|---|---|---|---|
Brick Apartment Building 17 Albatross St |
Dormitory/ Apartments |
Class I |
100% |
Yes |
0% |
Yes |
Brick Dorm 17 Albatross St |
Dormitory |
Class I |
100% |
Yes |
0% |
Yes |
David House 27 Albatross St |
Dormitory |
Class I |
100% |
Yes |
0% |
No (no fossil-fuel burning equipment) |
Drew House 8 North St |
Dormitory |
Class I |
100% |
Yes |
0% |
No (no fossil-fuel burning equipment) |
Ebert hall 24 MBL St |
Dormitory |
Class I |
100% |
Yes |
100% |
Yes |
11 North Street House |
Dormitory/ Apartments |
Local |
100% |
No |
0% |
Yes |
Smith Cottage 33 Bar Neck Rd |
Dormitory/ Apartments |
Class I |
100% |
No |
0% |
Yes |
Crane House 63 Millfield Street |
Dormitory/ Apartments |
Class I |
100% |
No |
0% |
Yes |
Swope Dorms (housing) 5 North St |
Dormitory |
Class I |
100% |
Yes |
0% |
No (no fossil-fuel burning equipment) |
Veeder House 25 Albatross St |
Dormitory |
Class I |
100% |
Yes |
0% |
No (no fossil-fuel burning equipment) |
Marshview Farm (Newburyport) |
Dormitory/ Apartments/ Laboratory |
Local |
100% |
Yes |
0% |
Yes |
Off Campus Cottages (72) |
Dormitory / Apartments |
Local |
100% |
No |
0% |
Yes |
MBL Campus Labs/Classroom/Non-Housing Facilities Fire Safety Systems:
Location | Primary Use | Alarm Systems | Beds Protected by Fire Detection Systems | Pull Stations Present | Beds Protected by Sprinkler Systems | Carbon Monoxide Detection |
---|---|---|---|---|---|---|
MRC 125 Water Street |
Laboratory |
Class I |
100% |
Yes |
100% |
No |
Collection Support Facility 131 Water Street |
Shops/ Trade |
Class I |
100% |
Yes |
0% |
No |
Swope Center (non-housing) 5 North Street |
Dining/ Registration / Meeting Space |
Class I |
100% |
Yes |
0% |
Yes |
Lillie - Crane Wing 7 MBL Street |
Laboratory |
Class I |
100% |
Yes |
0% |
No |
Lillie 7 MBL Street |
Laboratory / Library |
Class I |
100% |
Yes |
0% |
No |
Loeb 18 MBL Street |
Laboratory - Teaching |
Class I |
100% |
Yes |
100% |
No |
Rowe 10 MBL Street |
Laboratory |
Class I |
100% |
Yes |
100% |
No |
Starr 11 Albatross Street |
Laboratory/ Offices |
Class I |
100% |
Yes |
100% |
No |
Homestead 167 Water Street |
Offices/ Administrative |
Class I |
100% |
Yes |
0% |
No |
MBL Club 100 Water Street |
Retail / Meetings /Children Camp |
Class I |
100% |
Yes |
0% |
No |
Environmental Science Laboratory 175 Water Street |
Laboratory |
Class I |
100% |
Yes |
0% |
No |
Candle House 127 Water Street |
Office /Administrative/ Classroom |
Class I |
100% |
Yes |
0% |
No |
Broderick House 17 North Street |
Offices/ Administrative |
Class I |
100% |
Yes |
0% |
No |
15 North Street |
Laboratory/ Shop Trades |
Class I |
100% |
Yes |
0% |
No |
Periwinkle Camp Oyster Pond Road |
Children’s Camp |
Class I |
100% |
Yes |
0% |
No |